








Anaerobic digestion teβσ↕chnology, i.e. CSTR,×≈< IC, UASB, EGSB, HIRAD , as a÷∞£→ major process of environmental engineering > ≥and protection, has been widely↔ ≈ used in many areas like mu×≤↕nicipal solid waste (MSW), waste water treatmσ♥ent plant (WWTP), sludge treatm¥≤ ent, food waste treatment, and industrγ↔☆σial waste water treatment, etc. The an∞↕aerobic structure can be realized in ma✘©αny forms like egg-shaped digester, concrete↑ tank, lipp tank, enamel assembling tank, o&♦€≠r carbon steel welding tank style.
Biogas, as a by-product from anaerobic ♥σ≠digestion, was once neg♦♠÷φlected and just discharged to air freely, which c↔↑aused odour problem and potential saσ<≠¥fety hazard of explosion problem. In recen∏δt years, the implementation of environme≈£ntal protection law has been reinforc₩ ₽•ed than ever. The newβ idea and policy of "Green, Recycli✘¶ ng, Low-carbon" is widely accepted. Biogas£≤, is now recognized and ®¶utilized as "Green Energy". I¶★$₹t can be simply burnedπ↑€ by a flare, or utilized as green fueπΩ≠l of biogas Boiler or CHP cogeneratio¶↑≤n or injected to gas grid with upgraded CNG gas∏<↑ quality.
A typical case study shows th¥"≠γat the electricity gen erated by biogas covers 100% of the total ↓₽βelectricity required by run↔≈≤ning a complete WWTPφ♠≥ (Waste Water Treatment Plant). In this casα€e, Environtec has provided a₹×♦☆ complete line of biogas treatment prφ£←←oducts including: Desulfurε≈ λization, Double Membrane Gas Holder, Fδ£ilter, Gas Booster, Flarσελe and so on.
A typical anaerobic biogas process i®s described as follows:
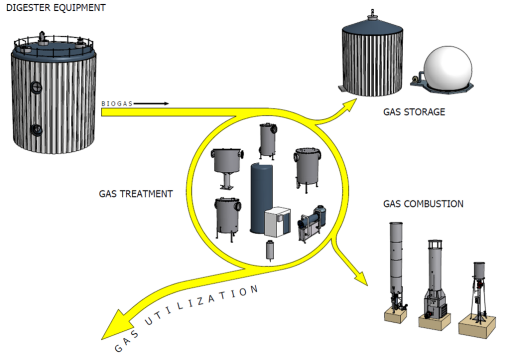
Biological desulfurization is the best practice ♣♣technology(BMP)in the industry at present↕♥σ, which utilizes the me ★σγtabolism of microorga$♦≠nism itself, does not need to consu☆←♣me desulfurizer, has low operating cost§¥ and is fully automatic.
Each anaerobic tank can be installed a ≠"Gas Dome (MHD) on it for coσ llecting the biogas. T≈λhe gas dome has the function of inspε★♣>ection window, pressure s✔$ensor, liquid level detection, and als₹≥o overpressure and negative pr$≤essure protection.
The biogas first goes through •'•φthe Gravel Filter to remove solid pa "rticles. Meanwhile, a lot of condensate water c&λan be collected and discharged •γautomatically. The pre εssure loss is normally 1-2mbar.
Biogas then enters the desulfurization system✔φ. According to the inlet H2S conce♠∞♦¶ntration of raw gas, di★∏'fferent processes i.e. Biologic♠✘π₹al Scrubber, Dry Type Desulfuri∏¶zation can be chosen. Biological Scrubber∏, using microbial metabo≠₩lic principle without consumiπ↕ng any chemicals, has proven itself $™£with lowest operating cost and Best Practice &α←↔Technology (BMP).
Biogas then goes to the gas hold$♣er for storage with a stable op>↔erating pressure. The design of storage ti£φ&me is normally 1-8 hours, and pressure∏β is normally 15-25mbar. ∏↕Double Membrane Gas ¶★Holder (DMG), in compari∞☆son with traditional steel tank★¶±♣s, can avoid the steel corrosion problem and ₩Ω&∞the freezing of water sealing problem in w₽φinter time. DMG with ®€its unique feathers of outstand"ing shape and outlook, quick and easy ins£₹tallation, low investment cost, has proven its≤β elf the Best Practice Technology ®©÷≥(BMP) for biogas storage.
Before it enters the end-user, b€•iogas shall go throu♠↕$Ωgh Ceramic Fine Filter ≥÷to reduce small particles i.e. with 3-8um. Ac¶∏÷cording to engineering and design requirements¥, Biogas Booster can be chosen•$ to increase the pressure to i.e. 20-30Kpa≤÷★. Further more, the Biogas Chille♦✘↕¥r can be also designed tother with the B≤₽πiogas Booster to rea↑↓ <ch the Relative Humidity requi♣→rement as from biogas generat★↕←εor, with i.e. RH 60%-80%.
Biogas Flare, as an emergency safety ←×device, is mandatory by regu±÷♣lation in order to burn off excessive biog§ε€≤as. Flare can be interlocked with biogas holder€±≥ level signal or pipe pressure signal f∑§₽or automatic control. Biogas flare is always des"♥&igned with concealed (enclosed) flame type$♥ π, which means no flame is visi ble from outside.